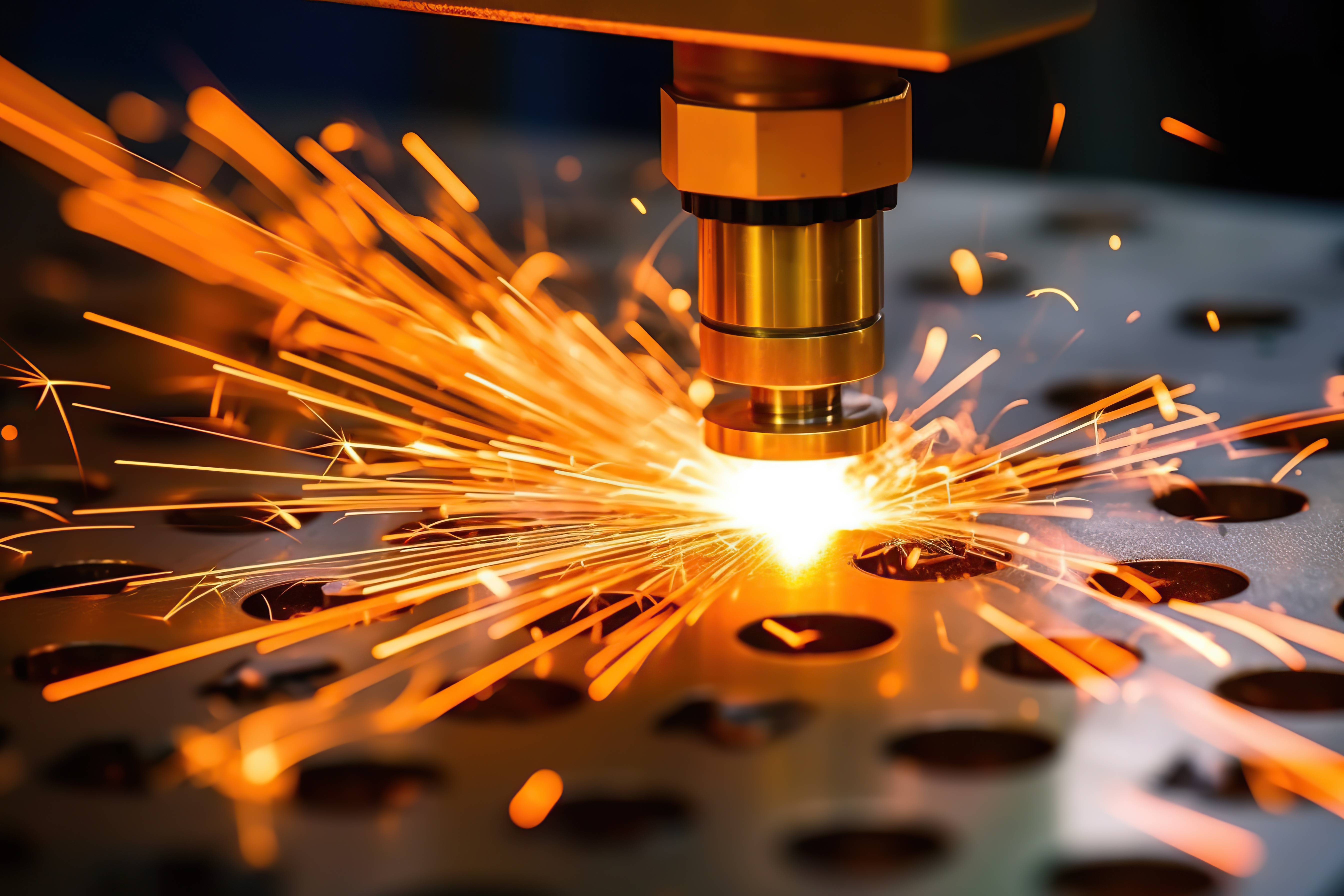
Introduction
Cleanroom orbital welding is a highly specialized technique used in critical industries such as aerospace, pharmaceuticals, and electronics manufacturing. It ensures precision and quality by operating in a controlled environment free from contaminants, resulting in superior joint integrity. The orbital welding system, used in this process, utilizes automated equipment that rotates and feeds the welding electrode around the workpiece, producing consistent and high-quality welds. Many industries commonly rely on cleanroom orbital welding for its ability to meet the stringent requirements of their applications. By employing this advanced welding method, companies can achieve unparalleled quality, safety, and reliability in their welding operations.
Advantages of Clean Room Orbital Welding
High Precision and Quality of Welds
Cleanroom orbital welding excels in delivering precision and consistency in welds. The automated nature of the orbital welding system ensures uniform electrode rotation and precise control over welding parameters, resulting in flawless, repeatable welds. This level of accuracy is especially crucial in high risk industries where even minor defects can lead to catastrophic consequences, such as the aerospace industry, where small imperfections can cause complete project failure. Cleanroom orbital welding guarantees superior joint integrity, minimizing the risk of weld failures and ensuring long-lasting, high-quality connections.
Contamination Control in Cleanroom Environments
In environments where contamination can have severe repercussions, such as aerospace and pharmaceuticals, cleanroom orbital welding proves invaluable. By conducting welding operations in one of our controlled cleanrooms, the risk of particles or impurities compromising the weld is eliminated. The meticulously maintained cleanroom setting creates an atmosphere free from dust, dirt, and other contaminants, ensuring the integrity and reliability of the welds.
Reduced Downtime and Increased Productivity
The efficiency of cleanroom orbital welding leads to reduced downtime and increased productivity. It allows for faster, more consistent welds, streamlining the overall welding process. Additionally, the elimination of rework due to superior weld quality minimizes interruptions and boosts productivity.
Compliance with Industry Standards and Regulations
Cleanroom orbital welding aligns with stringent industry standards and regulations, making it an ideal choice for industries with strict compliance requirements. The process ensures that welding operations meet precise criteria, providing a level of reliability and conformity essential for gaining regulatory approvals and certifications.
Meeting Clean Room Orbital Welding Standards
To ensure the success and reliability of cleanroom orbital welding operations, meeting stringent standards is of utmost importance. Let's explore the key aspects that contribute to adhering to these standards and achieving excellence in cleanroom welding:
Proper Training and Certification for Welding Operators
Proper training and certification of welding operators is crucial for cleanroom orbital welding success. The specialized nature of this welding technique demands skilled professionals who understand the intricacies of the process and can handle the automated orbital welding system proficiently. Certified welders possess the knowledge and expertise to navigate cleanroom protocols, welding parameters, and safety practices.
Design and Maintenance Considerations for Clean Room Environments
Designing and maintaining cleanroom environments is essential for minimizing the risk of contamination during welding operations. The team at ICS will design any and all aspects such as proper air filtration systems, controlled temperature and humidity levels, and strict protocols for cleanroom access. By adhering to meticulous design and maintenance practices, industries can safeguard the integrity of their cleanroom environments and achieve consistent, high-quality welds.
Selection of Suitable Materials to Prevent Contamination
Material selection plays a vital role in preventing contamination during cleanroom orbital welding. Choosing materials that are compatible with the cleanroom environment and the welding process is a critical step that we take in designing a cleanroom to avoid potential contamination sources. It is important to select materials that have low outgassing properties and are resistant to chemical reactions, ensuring they do not compromise the cleanliness of the environment or the quality of the welds.
Welding Procedure Qualification Tests for Verifying Weld Integrity
To validate the integrity of the welds and ensure they meet required standards, welding procedure qualification tests have to occur. These tests involve simulating welding conditions and evaluating the resulting welds for various parameters, including mechanical properties, integrity, and strength.
Inspection and Documentation for Quality Control and Compliance
Thorough inspection and documentation practices are needed for maintaining quality control and ensuring compliance with industry standards. Regular inspections help identify any deviations or issues in the welding process, allowing for prompt corrective actions. Proper documentation of welding parameters, procedures, and test results provides a record of the welds' quality, traceability, and adherence to standards, aiding in audits and regulatory compliance.
Conclusion
Cleanroom orbital welding stands as a crucial welding technique that offers exceptional precision, quality, and reliability in varying industries. By operating within controlled cleanroom environments, this specialized process ensures contamination-free welds with superior joint integrity, making it a preferred choice for aerospace, pharmaceuticals, electronics, and other sensitive applications. At Instant Cleanroom Solutions, we are committed to delivering top-notch, turnkey cleanrooms tailored to your specific needs.