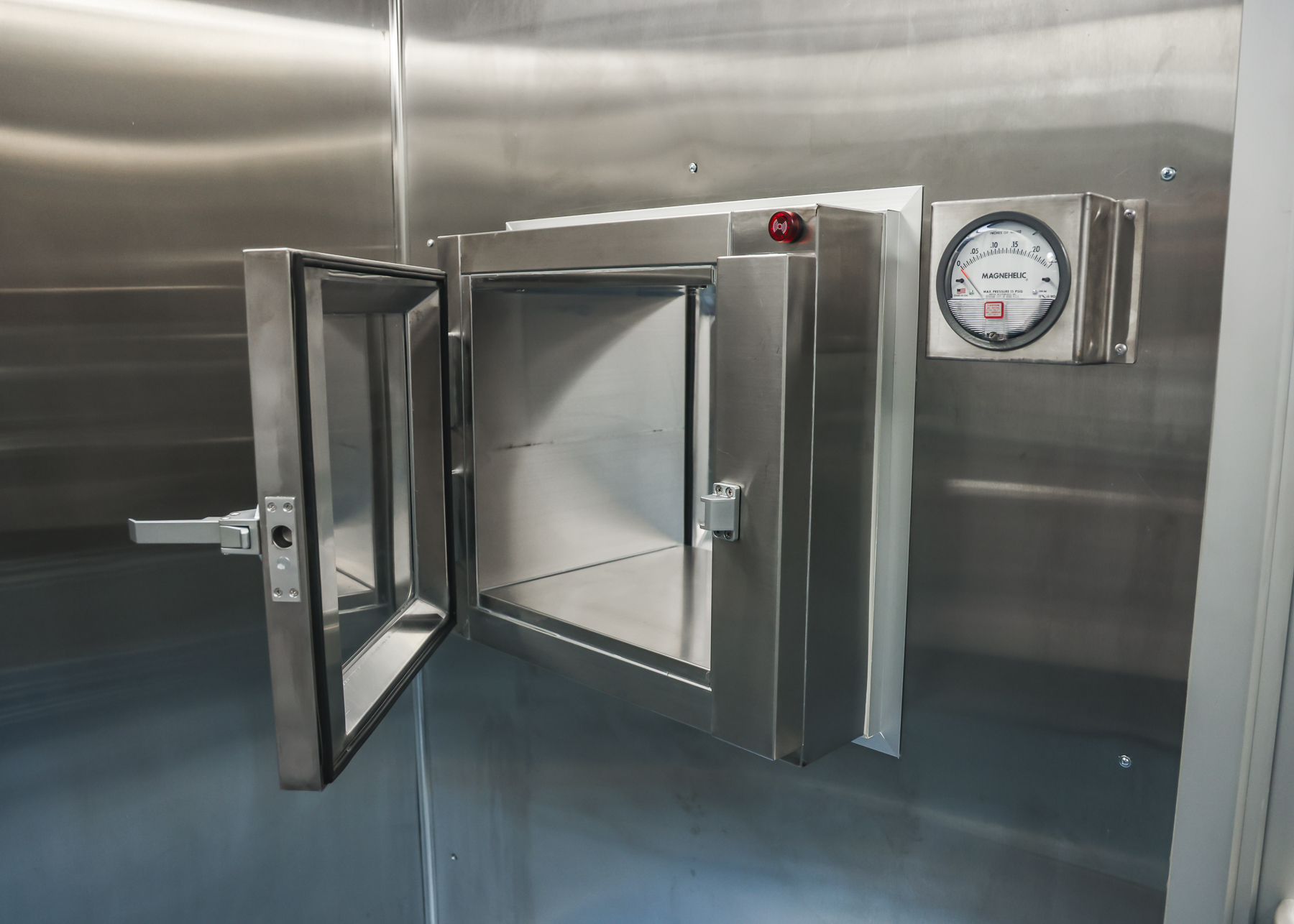
How to Effectively Use Pass-Through Chambers in Cleanrooms
Pass-through chambers serve as an integral component within cleanroom environments, playing an important role in maintaining the integrity of controlled spaces. These specialized chambers enable the transfer of materials and equipment between different areas of varying cleanliness levels, while minimizing the risk of contamination. Pass-through chambers provide a barrier against particulate and microbial contamination, ensuring the preservation of product quality, process integrity, and personnel safety. In this post, we will dive into the fundamental principles behind pass-through chambers, explore their various configurations, and highlight their key applications in cleanroom environments.
Understanding Pass-Through Chambers
A pass-through chamber, also known as a transfer hatch or transfer chamber, is a specialized enclosure designed to facilitate the controlled transfer of materials and equipment between two areas of differing cleanliness levels. It serves as a physical barrier that minimizes the risk of contamination during the transfer process. There are several types of pass-through chambers available, each designed to meet specific requirements. Mechanical pass-through chambers feature manual doors that require physical interaction for access, whereas airlock pass-through chambers employ air pressure differentials to prevent cross-contamination. Interlocked pass-through chambers utilize electronic interlocking mechanisms to ensure that only one door can be opened at a time.
Pass-through chambers are equipped with high-quality gaskets and seals to maintain airtight conditions and prevent the ingress of contaminants; most pass-through chambers are constructed using durable materials that are easy to clean and chemically resistant, such as stainless steel.
Applications of Pass-Through Chambers in Cleanrooms
Contamination control and prevention
Pass-through chambers effectively minimize the risk of cross-contamination between areas of varying cleanliness levels. By allowing materials to be transferred without direct human contact, they reduce the potential for microbial and particulate contamination. This ensures the integrity of both the source and destination areas, safeguarding the quality of products and preserving the overall cleanliness of the cleanroom environment.
Efficient workflow management
Pass-through chambers streamline the flow of materials, components, and tools between different cleanroom areas. They provide a designated passage for materials to move smoothly from one environment to another, eliminating the need for personnel to enter multiple areas. This optimized material flow reduces the risk of contamination caused by human traffic and enhances operational efficiency.
Enhancing productivity and safety
With their well-designed doors and airtight seals, these chambers enable quick and reliable transfer processes. This convenience accelerates material handling, saving time and effort while minimizing personnel entry into controlled areas, thus reducing the potential exposure to hazardous substances or environments. This not only ensures the well-being of cleanroom operators but also safeguards the integrity of sensitive processes and products.
.png)
Factors to Consider for Effective Pass-Through Chamber Usage
Design considerations
Pass-through chambers should be selected based on their size and dimensions to align with the specific needs of the cleanroom layout. They must fit seamlessly within the available space and facilitate efficient material transfer without obstructing workflow or impeding personnel movement.
The materials used in constructing pass-through chambers should be carefully chosen to ensure compatibility with cleanroom standards. Commonly, stainless steel is preferred due to its durability, ease of cleaning, and resistance to chemical agents. It is essential to select materials that are non-shedding, easy to decontaminate, and compliant with cleanroom cleanliness requirements, likely matching wall construction materials with chamber construction materials.
Airflow management and pressure differentials
Pass-through chambers should be designed to minimize disruption to the cleanroom's airflow patterns and pressure differentials. Proper sealing and integration with the cleanroom HVAC system help maintain the desired air balance, minimizing the risk of turbulence that can potentially introduce contaminants. Ventilation, air filtration, airflow patterns, and pressure differentials need to be considered during the design and installation process to uphold the desired cleanliness levels.
Security measures
Incorporate robust access control mechanisms in pass-through chambers to prevent unauthorized entry and minimize the risk of contamination. This can include interlocking doors that allow only one door to be open at a time, electronic locks, key card access systems, or biometric authentication methods. Implement monitoring systems and audit trails within pass-through chambers to enhance traceability and accountability. These systems can record the date, time, and identity of individuals accessing the chambers, providing a valuable record for quality control purposes and identifying potential sources of contamination.
Best Practices for Pass-Through Chamber Integration
- Proper installation and positioning: Pass-through chambers should be installed by trained professionals, considering factors such as cleanroom layout, workflow efficiency, and adherence to cleanroom standards. Positioning the chambers strategically, with easy access for authorized personnel, minimizes the risk of contamination and facilitates smooth material transfer.
- Regular maintenance and cleaning procedures: Establishing a routine maintenance schedule is crucial for pass-through chamber upkeep. Regular cleaning, disinfection, and inspection of the chamber and its components, including seals, gaskets, and filters, should be conducted to maintain cleanliness and functionality. This ensures that the chambers remain in optimal condition and continue to provide reliable contamination control.
- Training and educating cleanroom personnel: Personnel should be familiarized with usage protocols, including proper hand hygiene, correct handling of materials, and adherence to access control mechanisms. This ensures that operators understand the importance of maintaining cleanliness, minimizing contamination risks, and maximizing the benefits of pass-through chambers.
Conclusion
Pass-through chambers are essential tools for maintaining the integrity and cleanliness of controlled environments by providing a reliable barrier against particulate and microbial contamination and ensuring the preservation of product quality, process integrity, and personnel safety. When effectively used, pass-through chambers contribute to contamination control and prevention, efficient material flow, and overall cleanliness. If you think a pass-through chamber will enhance your cleanroom operation, contact Instant Cleanroom Solutions for expert advice and customized designs.
This article is for informational purposes only and should not replace professional or regulatory guidance.