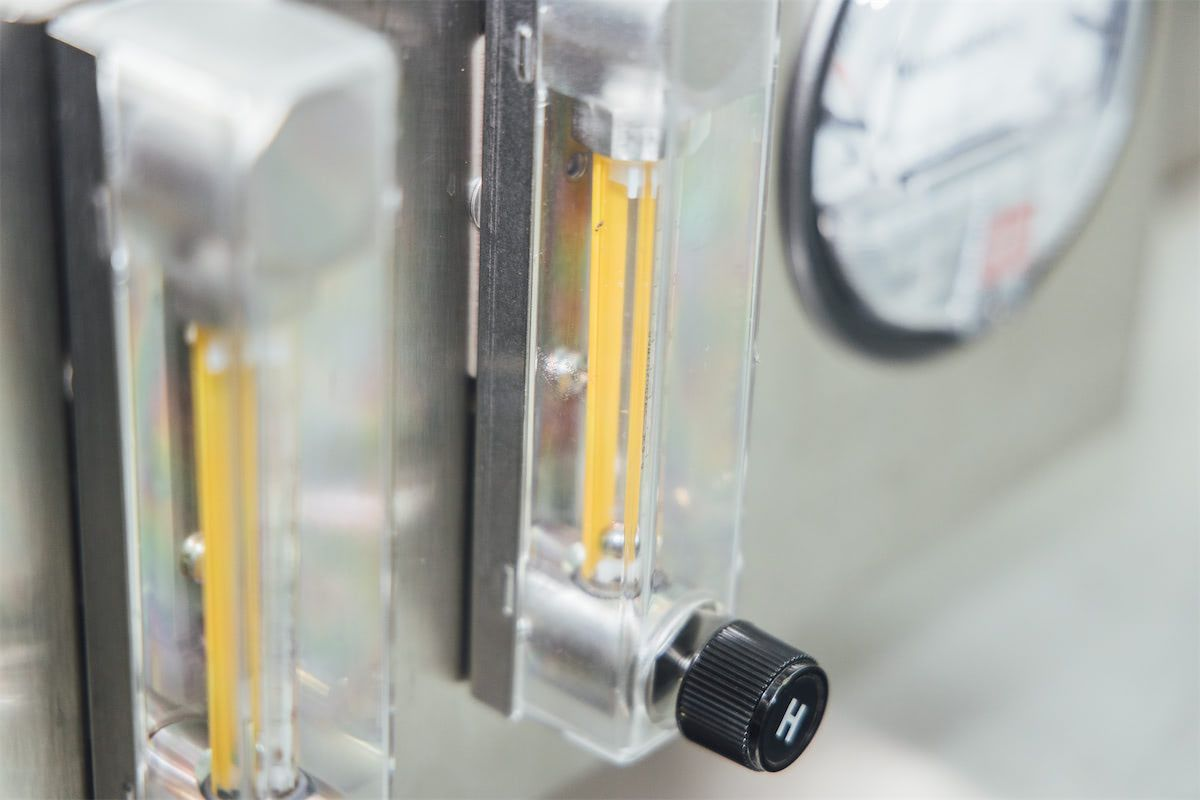
Understanding Pressure Cascades
Cleanrooms are highly controlled environments designed to minimize the presence of airborne particles, contaminants, and other impurities. They play a crucial role in various industries where precision, quality, and sterility are paramount. Positive and negative pressure cascades are used in cleanroom design to control the flow of contaminants or hazardous material. In this article, we will explore the differences between positive and negative pressure cascades to help you determine which is best for your cleanroom.
Positive Pressure Cleanrooms
Positive pressure cleanrooms are designed to maintain a higher pressure inside the cleanroom compared to the surrounding areas. By keeping the pressure inside the cleanroom higher, air naturally flows outwards, creating a barrier against particles, dust, and other pollutants that may be present in the external environment.
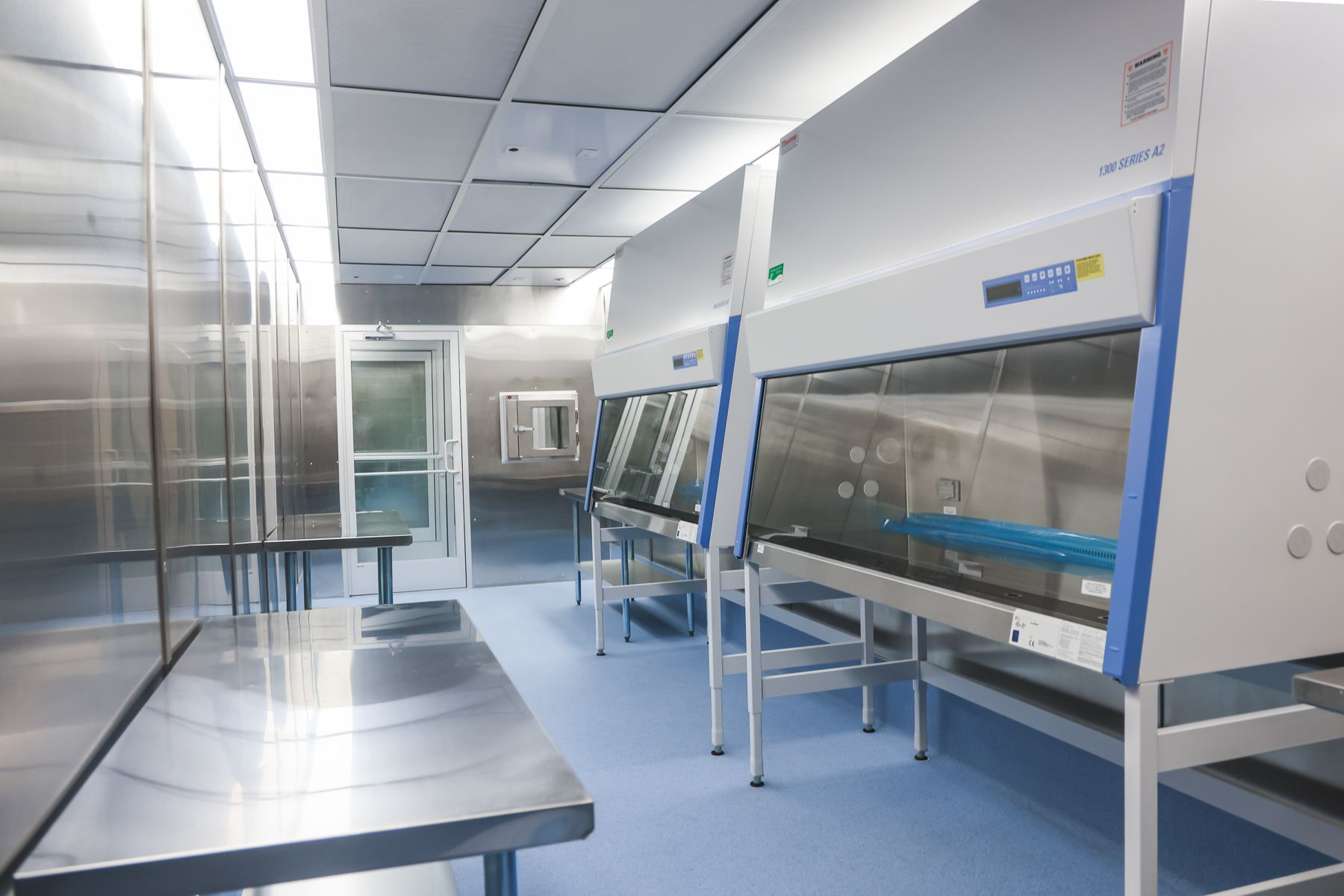
Components and Features
- Air handling units (AHUs) condition and filter the air that enters the cleanroom environment. Standard cleanroom AHUs include high-efficiency particulate air (HEPA) or ultra low particulate air (ULPA) filters.
- Airflow patterns and direction are carefully designed to facilitate the positive pressure cascade. Typically, air is supplied from the AHUs at a higher pressure than the surrounding areas and moves towards the cleanroom's exits. This prevents contaminants from entering the cleanroom by effectively pushing them away in a continual purge.
- Control mechanisms such as pressure sensors, variable speed fans, and dampers are employed to maintain the desired pressure differentials throughout the cleanroom by sensing potential pressure changes and adjusting airflow to compensate.
Industries
Positive pressure cleanrooms are extensively utilized in various industries where contamination control is crucial. The industries that commonly employ positive pressure cleanrooms include pharmaceutical manufacturing, microelectronics and semiconductor production, as well as biotechnology and medical device manufacturing.
- Pharmaceutical manufacturing: positive pressure cleanrooms are vital for ensuring the sterility and integrity of drug products. The positive pressure environment helps prevent the ingress of contaminants, safeguarding the quality and efficacy of pharmaceuticals.
- Microelectronics and semiconductor: rely on positive pressure cleanrooms to maintain particle-free environments during the fabrication of sensitive electronic components. When manufacturing at the micro-scale, the presence of airborne particles could catastrophically compromise the performance of microchips and semiconductors.
- Biotechnology and medical device manufacturing: These industries require controlled environments to maintain the purity and sterility of products. Positive pressure helps protect sensitive biological materials and medical devices from external pollutants, ensuring their safety and reliability.
Negative Pressure Cleanrooms
Negative pressure cleanrooms are designed to maintain a lower pressure inside the cleanroom compared to the surrounding areas to contain hazardous substances and infectious agents. By maintaining lower pressure inside the cleanroom, any potential leaks or releases are inward. Contaminated air is then filtered and recycled, creating a closed system that has no interaction with the surrounding environment. This is particularly crucial in biological research laboratories, chemical and pharmaceutical containment facilities, as well as quarantine and isolation units.
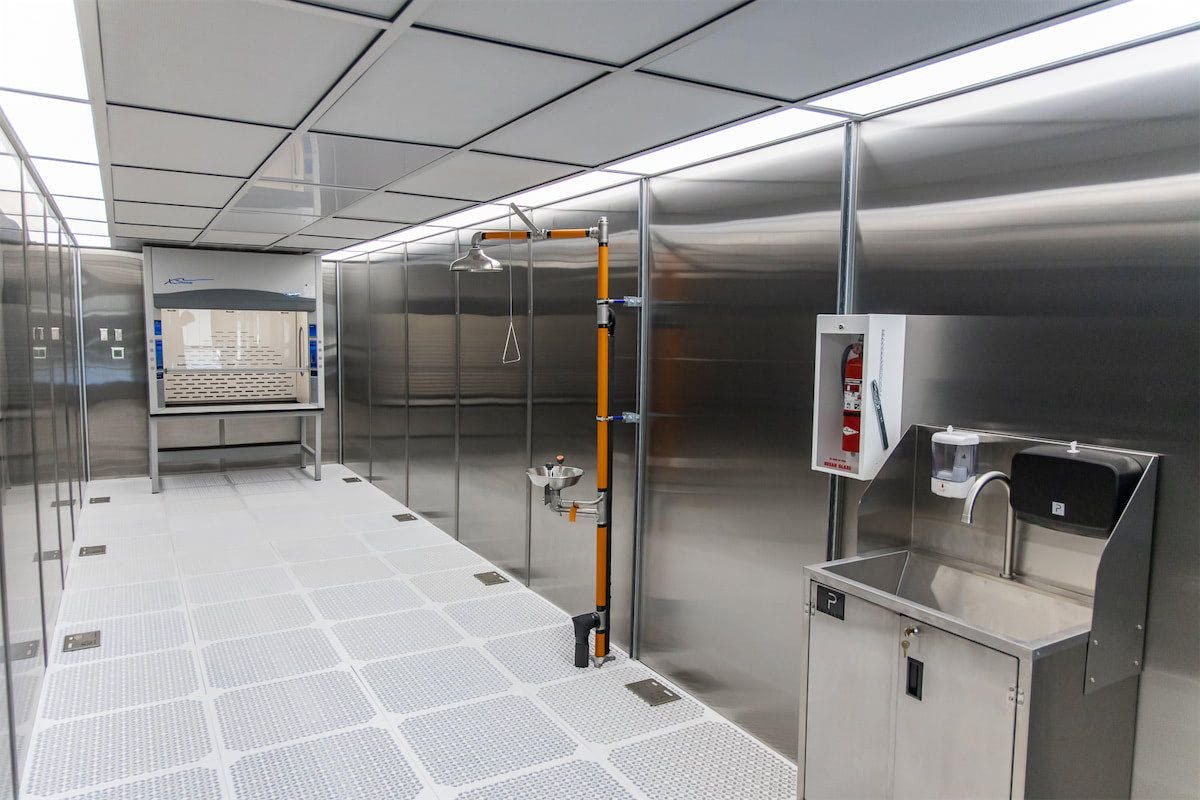
Components and Features
- Exhaust and air filtration systems remove air from the cleanroom and ensure it is properly filtered before being discharged or recyled. Filtration occurs through AHUs like HEPA and ULPA filters.
- Isolation chambers act as transition areas between different pressure zones, preventing direct airflow between them. Airlock systems allow personnel or materials to enter or exit the cleanroom without disrupting the pressure differentials.
- Moitoring and control mechanisms like pressure sensors and dampers ensure that the cleanroom remains at a lower pressure through pressure monitoring and airlfow control.
Industries
Negative pressure cleanrooms are extensively utilized in various industries that require containment and isolation of hazardous substances, pathogens, or contaminants. Industries that commonly use negative pressure in cleanrooms include biological research laboratories, chemical and pharmaceutical containment facilities, as well as quarantine and isolation units.
- Biological research laboratories: employ negative pressure cleanrooms and biological safety labs to prevent the release of potentially harmful biological agents and ensure containment during experiments involving genetically modified microorganisms.
- Chemical and pharmaceutical containment facilities: utilize negative pressure cleanrooms to prevent the escape of hazardous substances, such as toxic chemicals or potent pharmaceutical compounds as well as closed system filtration to protect working personnel.
- Quarantine and isolation units: contain and isolate patients with infectious diseases to prevent the spread of airborne pathogens beyond the designated area, minimizing the risk of cross-contamination.
Choosing the Right Pressure Gradient
When deciding between a positive pressure cleanroom and a negative pressure cleanroom, start by assessing specific requirements and environmental considerations. This article is written for general information. You should make sure to seek to professional guidance about your requirements. Determine the criticality of contamination control and the level of protection needed for your processes or products. If particle control is crucial, a positive pressure system is likely required, where a negative pressure cleanroom will almost always be used when hazardous agents or pathogens are present.
Further information will be gained by performing a thorough risk assessment to identify potential contaminants and their sources. Consider the nature of the work being conducted and the materials involved. This assessment will help determine if containment or isolation is a priority and ensure the cleanroom is designed to comply with regulations and industry standards. Evaluate the initial investment costs, maintenance requirements, and ongoing operational expenses associated with each type of cleanroom. Consider factors such as energy consumption, maintenance of airflow systems, and the need for specialized equipment.
Conclusion
Understanding pressure cascades is essential in designing cleanrooms that meet the specific requirements of different industries. Positive pressure cleanrooms maintain higher pressure inside to prevent the entry of contaminants, making them ideal for pharmaceutical manufacturing, microelectronics, and biotechnology industries. Negative pressure cleanrooms maintain lower pressure to contain hazardous substances and pathogens, making them crucial in biological research laboratories, chemical and pharmaceutical containment facilities, and quarantine units. By implementing the appropriate pressure differentials, cleanrooms effectively manage contamination control and safeguard sensitive processes, ultimately contributing to the success and reliability of various industries.