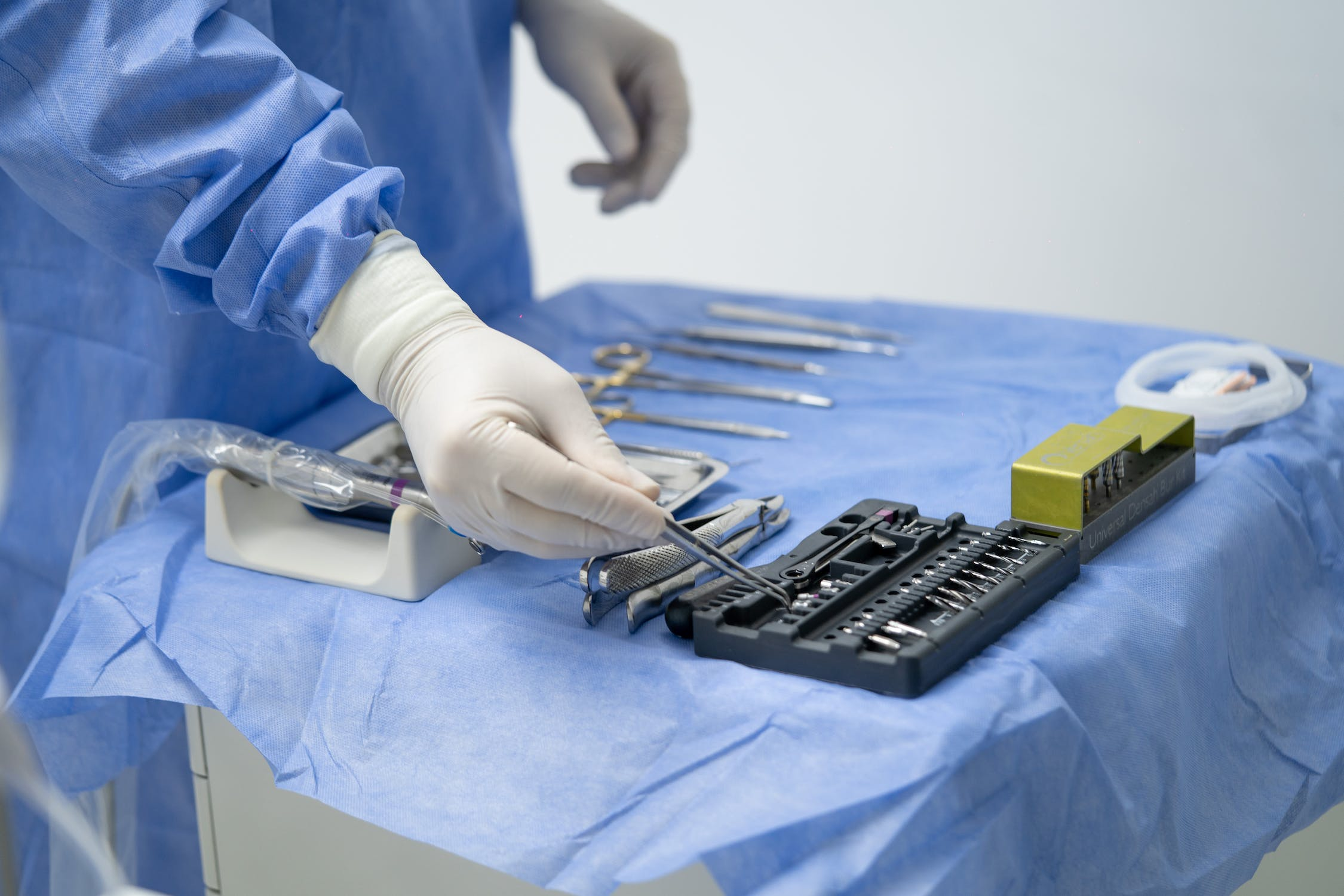
Comprehensive Guide to Cleanroom Design for Hospitals and Healthcare Facilities
The Importance of Cleanroom Design in Healthcare
Cleanrooms are critical in hospitals and healthcare facilities, as they provide a controlled environment to reduce the risk of contamination and infection. They are essential in various applications, including surgery, pharmaceutical manufacturing, and research laboratories. In this article, we delve into the fundamental aspects of cleanroom design for healthcare settings and offer practical advice for designing and maintaining these critical spaces.
Cleanroom Classifications: Understanding the Different Levels
ISO 14644-1 Classification
The International Organization for Standardization (ISO) developed the ISO 14644-1 standard, which classifies cleanrooms based on air cleanliness levels. There are nine classes, with ISO Class 1 being the cleanest and ISO Class 9 the least clean. Hospitals and healthcare facilities must adhere to these classifications when designing their cleanrooms. Most hospital settings require ISO Class 7 or Class 8 cleanliness, but occasionally, a more sterile environment can be necessary.
US FED STD 209E Classification
The United States has its classification system, known as the Federal Standard 209E. This system ranks cleanrooms from Class 1 (cleanest) to Class 100,000 (least clean). Although no longer the primary method of classification, these classes are often used in older written specifications in conjunction with ISO classifications and should be kept in mind.
Key Components of Cleanroom Design
Airflow and Ventilation
Proper airflow and ventilation are crucial for maintaining a cleanroom's desired cleanliness level. Designing an effective air management system involves:
- Air Filtration: High-efficiency particulate air (HEPA) filters or ultra-low particulate air (ULPA) filters are installed to remove contaminants from the air.
- Air Change Rate: The frequency of air changes per hour (ACH) should be determined based on the cleanroom's classification and application.
- Airflow Patterns: Unidirectional (laminar) or non-unidirectional (turbulent) airflow patterns should be designed according to the cleanroom's requirements, with the majority of cleanroom applications requiring laminar flow design.
Temperature and Humidity Control
Controlling temperature and humidity is essential for maintaining product quality, preventing microbial growth, and ensuring occupant comfort. Design considerations include:
- Temperature Range: Determine the optimal temperature range for the cleanroom's specific application.
- Humidity Range: Establish the appropriate humidity range to prevent condensation and microbial growth.
- Control Systems: Install accurate and reliable temperature and humidity control systems to maintain desired conditions.
Construction and Materials
The selection of construction materials and finishes for cleanrooms is vital for preventing contamination and ensuring durability. Considerations include:
- Wall, Ceiling, and Floor Materials: Choose non-porous, non-shedding, and easy-to-clean materials such as stainless steel, epoxy-coated surfaces, or high-pressure laminates.
- Furniture and Equipment: Select furniture and equipment that meet cleanroom requirements and can withstand frequent cleaning and disinfection without shedding particulates.
- Airlocks and Pass-Throughs: Design airlocks and pass-through chambers to minimize air turbulence and prevent cross-contamination. Many will be used to maintain a pressure cascade within the cleanroom. Learn more about negative vs. positive pressure cleanrooms to see what is required for your controlled environment.
Personnel and Material Flow
Proper personnel and material flow are essential for maintaining cleanroom integrity. Design strategies include:
- Access Control: Implement access control systems to restrict entry to authorized personnel only and to regulate the movement of those personnel to maintain pressure cascades.
- Gowning Procedures: Establish gowning protocols to minimize contamination introduced by personnel, clothing, or other particulate shedding material.
- Material Transfer: Design material transfer processes to prevent cross-contamination between clean and non-clean areas.
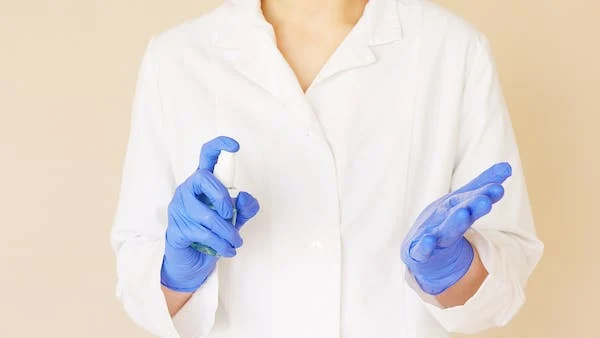
Cleanroom Maintenance and Monitoring
Routine maintenance and monitoring are crucial for ensuring cleanroom performance and compliance. Key aspects include:
- Cleaning and Disinfection: Implement a rigorous cleaning and disinfection program tailored to the cleanroom's application and classification.
- Airborne Particle Monitoring: Continuously monitor airborne particle levels to ensure compliance with cleanroom classifications and promptly identify potential contamination issues.
- Environmental Monitoring: Routinely measure temperature, humidity, and other environmental parameters to maintain optimal conditions and ensure regulatory compliance.
- Personnel Training: Provide ongoing training for cleanroom personnel to ensure they understand and adhere to proper gowning, cleaning, and operational procedures.
- Maintenance and Calibration: Regularly maintain and calibrate cleanroom equipment, including air filtration systems, temperature and humidity controls, and monitoring devices, to ensure reliable performance.
Understanding Hospital Applications
Within hospitals, there will be three main areas that utilize specially designed HEPA filters rooms.
- Operating rooms: Use HEPA filtration that is directed over the surgery area to provide fresh air cascading over the patient.
- USP 797 and USP 800 Compounding Rooms: A USP 797 lab will be a positive pressure cleanroom that is focused on product protection and used for sterile compounding of non-hazardous drugs. The USP 800 lab will be a negative pressure cleanroom used for handling hazardous drugs, such a chemotherapy, that is focused on both product protection and personnel protection.
- Pathology Labs: Utilize HEPA filtration and negative pressure to protect the personal that are analyzing patient blood work and other pathogens. The pathology lab will also utilize a biological safety cabinet that will protect the sample under investigation and the operator that is analyzing the sample. This will commonly be classified as a Biological Safety Level Two lab (BSL-2) according to the CDC.
Choosing the Cleanroom
It is important to select a provider who is able to meet your needs and has extensive experience in the field. Instant Cleanroom Solutions provides both hardwall — including temporary Mobile Cleanrooms and permanent Modular Cleanrooms — and the softwall Instant Cleanroom. Check out this post on hardwall vs. softwall cleanrooms to learn more about which option is best for your healthcare needs.
Conclusion
Designing and maintaining an effective cleanroom in hospitals and healthcare facilities is a complex process that requires careful consideration of numerous factors. By understanding cleanroom classifications, implementing appropriate design elements, and adhering to stringent maintenance and monitoring protocols, healthcare organizations can ensure their cleanrooms meet regulatory requirements, reduce the risk of contamination, and ultimately contribute to improved patient outcomes.